The saya is the wooden sheath the katana fits into. They are usually made out of soft wood and painted or laquered, and decorated with fantastic artistry. I’m a woodworker, not a painter. I make mine of of hardwood and let the wood grain speak for itself.
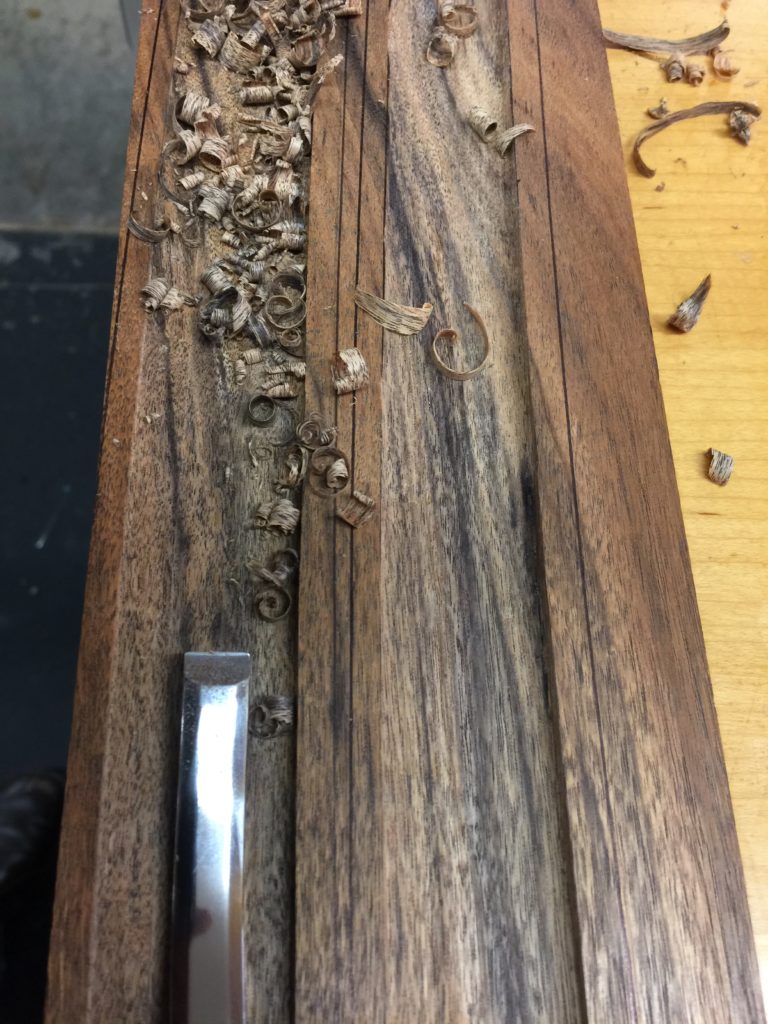
Saya are hand carved. This is again another instance of once thinking I could buy cool power tools and do all this easily but I still use hand tools to do it. I’m making this one from African rosewood. It was hard as a fricking rock and difficult to carve and probably ruined a couple of chisels, but it is a beautiful and strong wood.
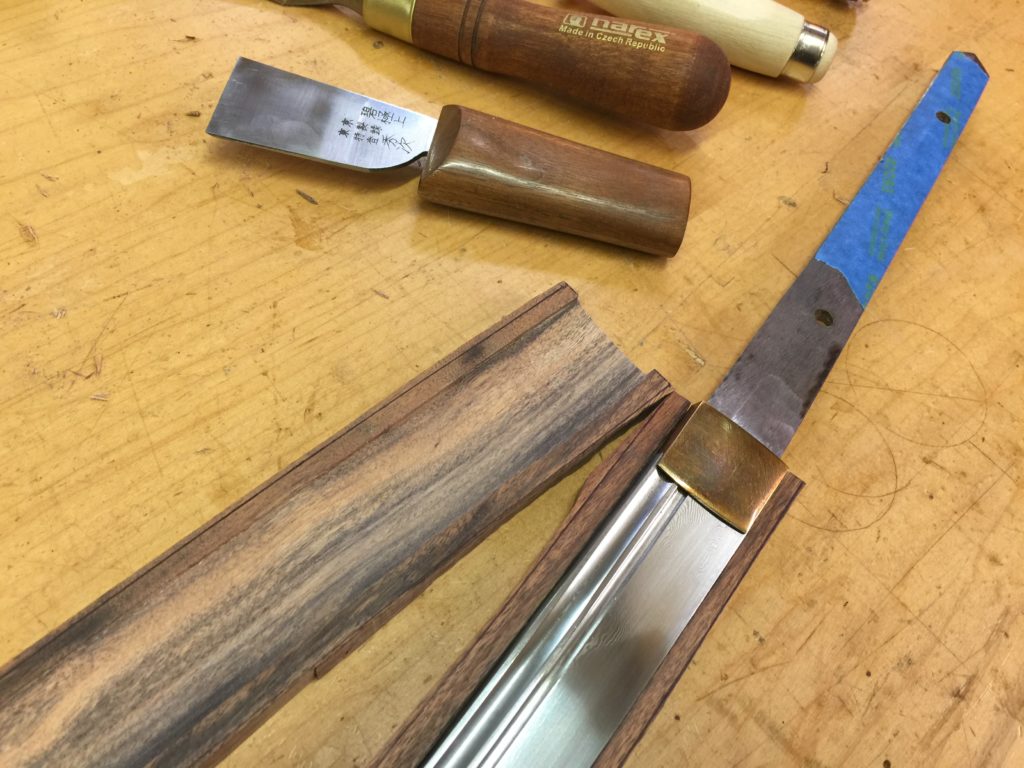
I light a snug fit. Too tight, and the blade won’t come out very quickly. Too loose, and it rattles around. There’s not a lot of room for error on these. I was a little nervous making this one, all the cuts needed to be on point, and if I screwed up I’d be carving a new saya.
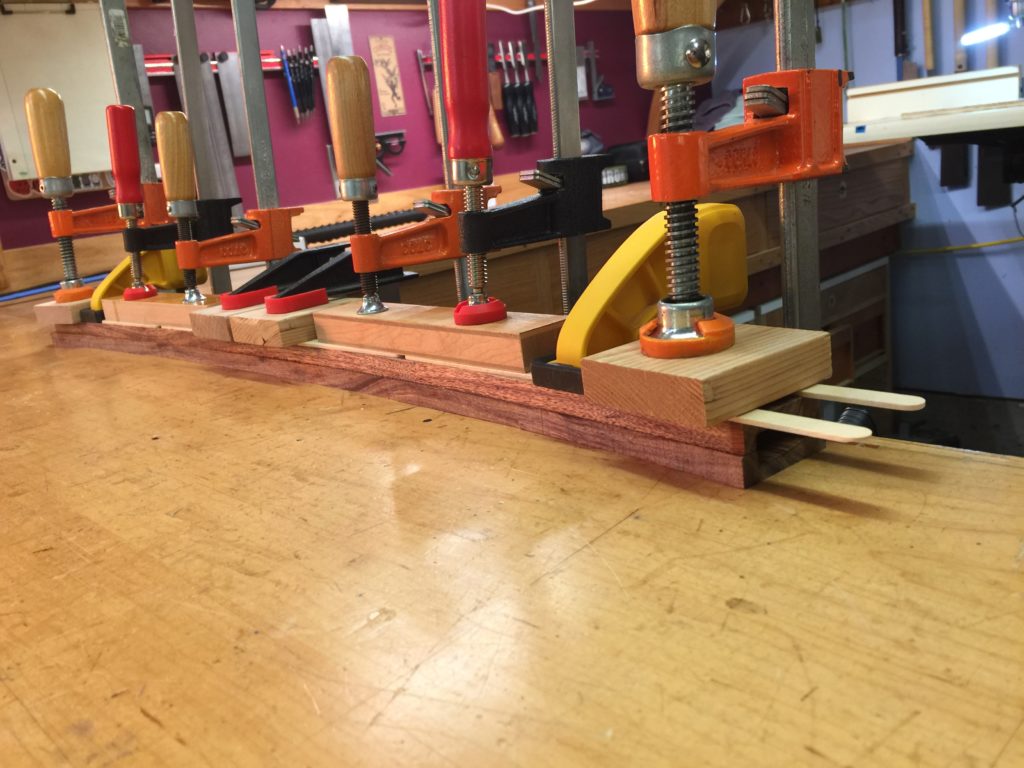
All clamps on deck for the glue up. You may notice I used popsicle sticks in the above pic. Placing them near the edge like that transfers the pressure to the outside of the saya, where the glue joint is. The middle is hollow and I don’t need the pressure there. Yeah, it’s a pain, but it makes for a good glue joint.
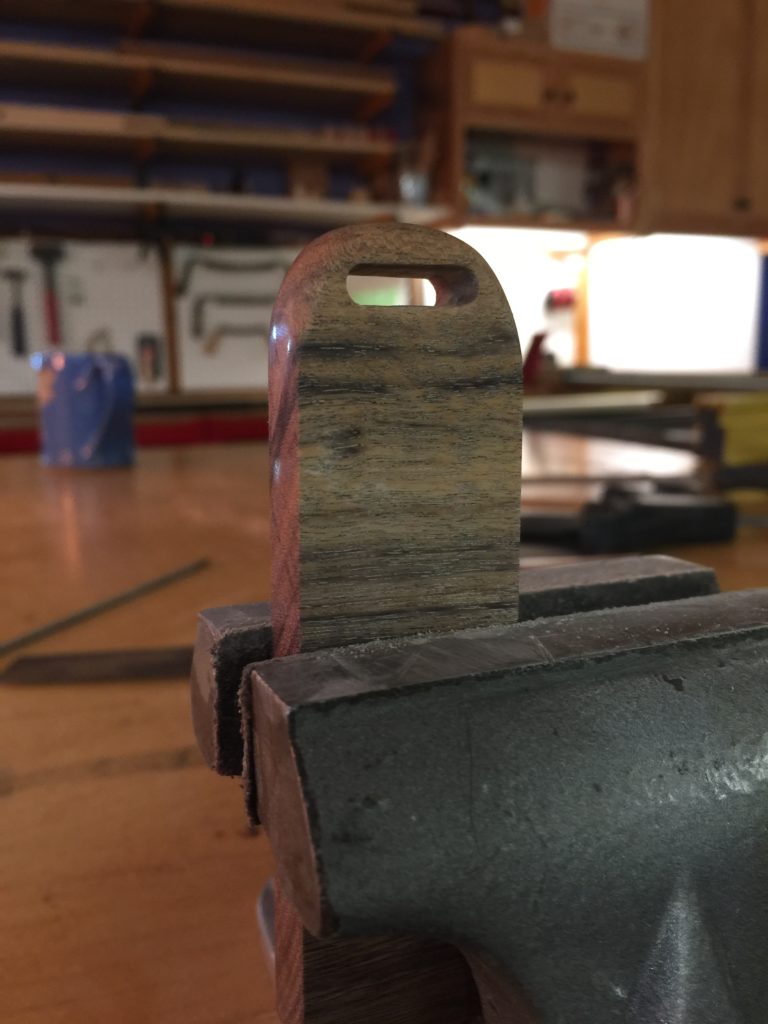
This is the kurikata, the little knob on the side of the saya that keeps it from falling through your belt. I make mine a little small, just what’s needed, and suited for a quick, light sword.
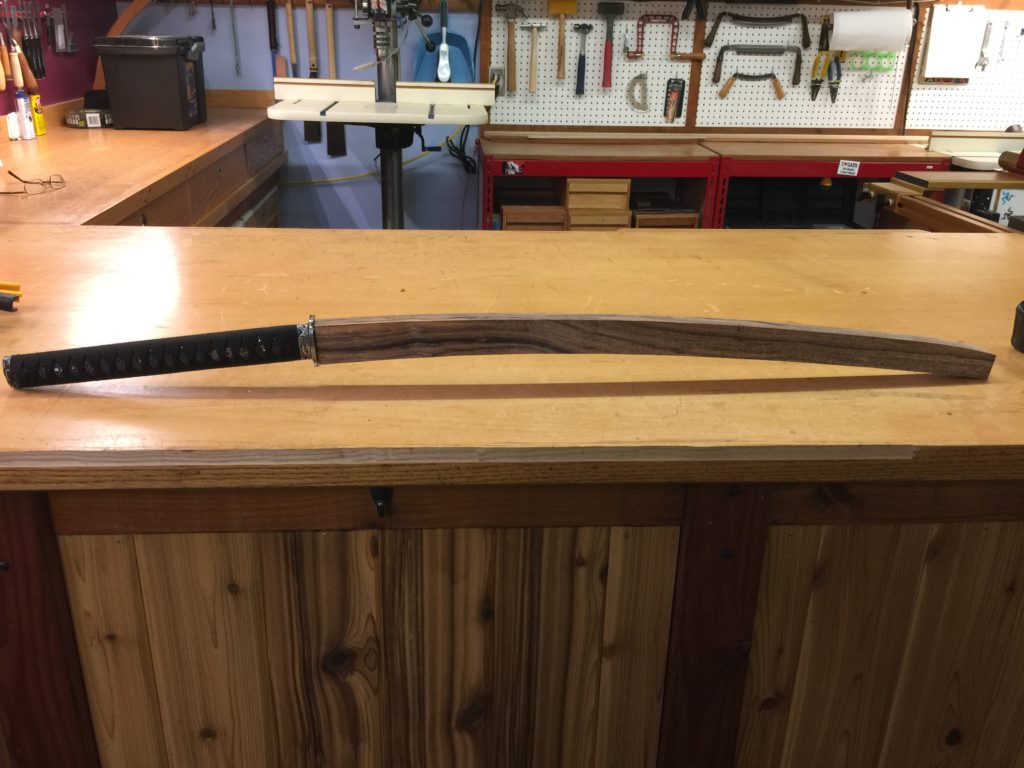
There’s always a little nervousness when the saya is first glued up. If for whatever reason it’s too tight, it is a real pain to make the inside any bigger. You literally have to tape sandpaper to your sword and slowly sand the opening larger until the fit is just right. It takes hours, if not days. Better to just get it right on the first try. This burden is only on those of us who make our saya as snug as I do. Traditionally, they are made a little loose and you don’t have to worry about this.
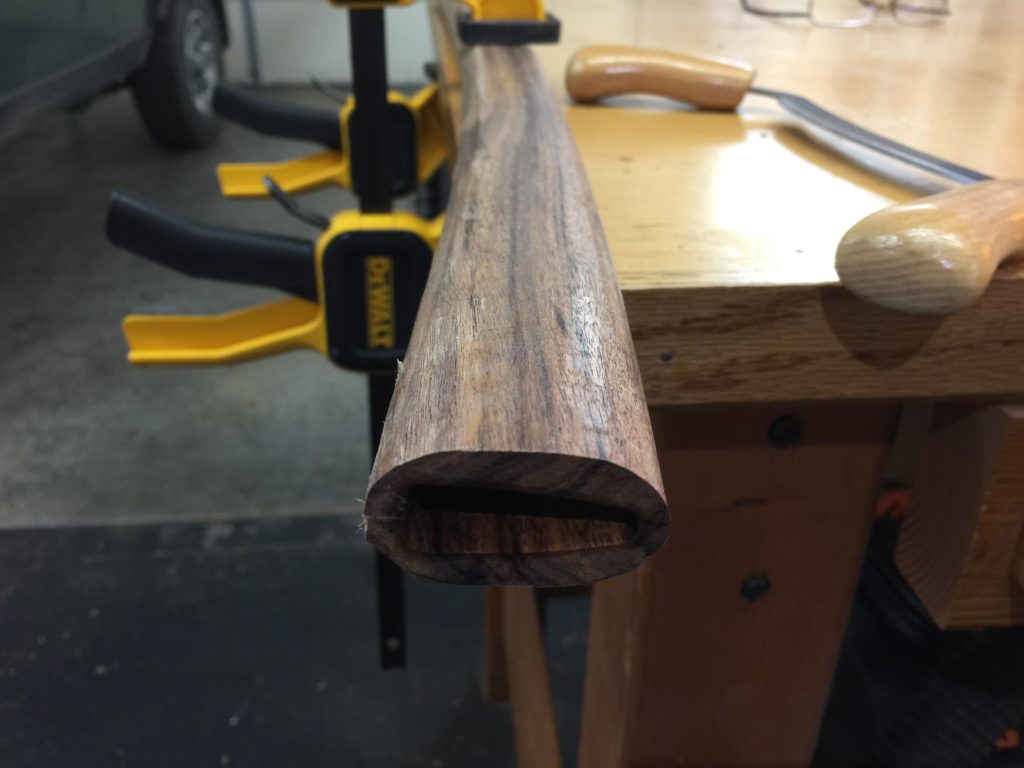
Carving this wood was a bear of a task. Draw knives, shavers, whatever I could use to get this nice oval shape, and then a course of sanding (for four hours) to get it all smooth.

It’s a nice fit, though, and all that sanding got the saya as smooth as glass. Traditionally, saya have a carved buffalo horn around the opening there, to help prevent the blade from wearing the wood down. But this wood is hard enough to withstand training, it won’t split like softwoods will.
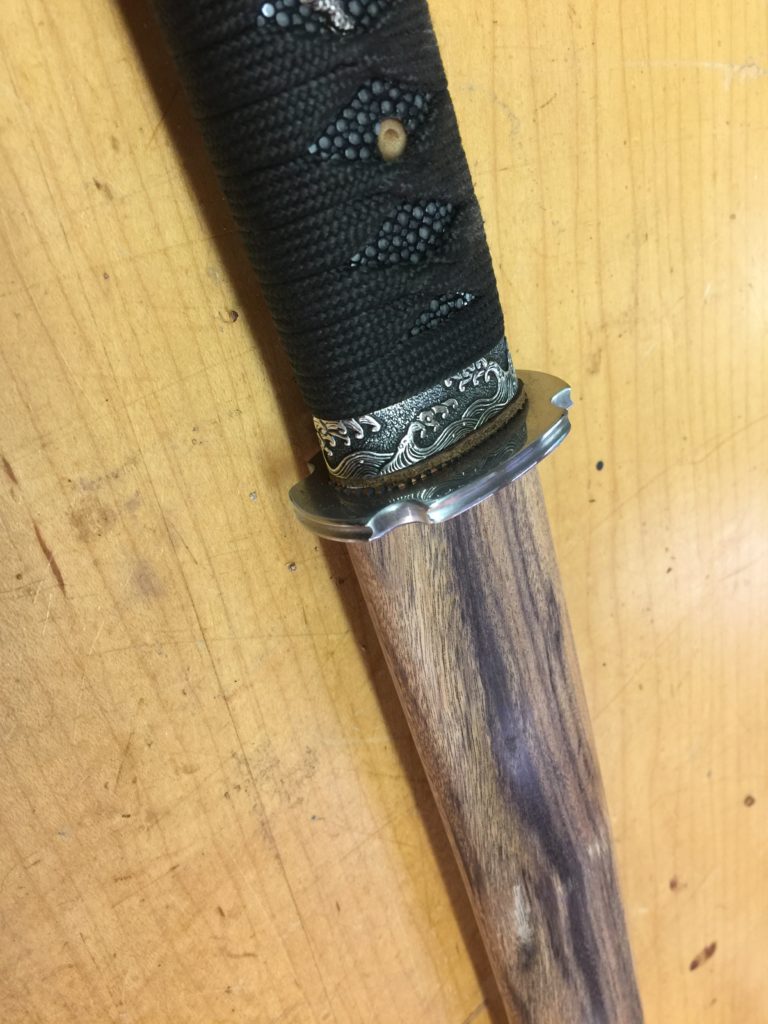
I really do like the bare wood much better than a lacquered or decorated saya. The traditional ones are beautiful, for sure, but I prefer mine.
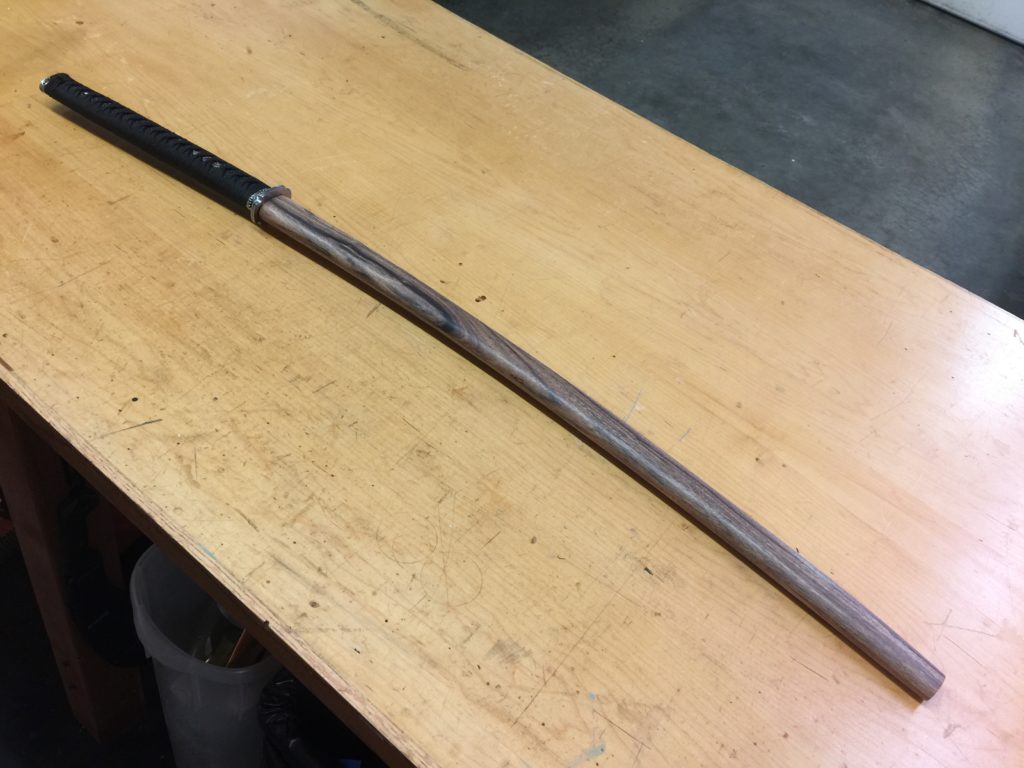
Slender and light, built for speed.
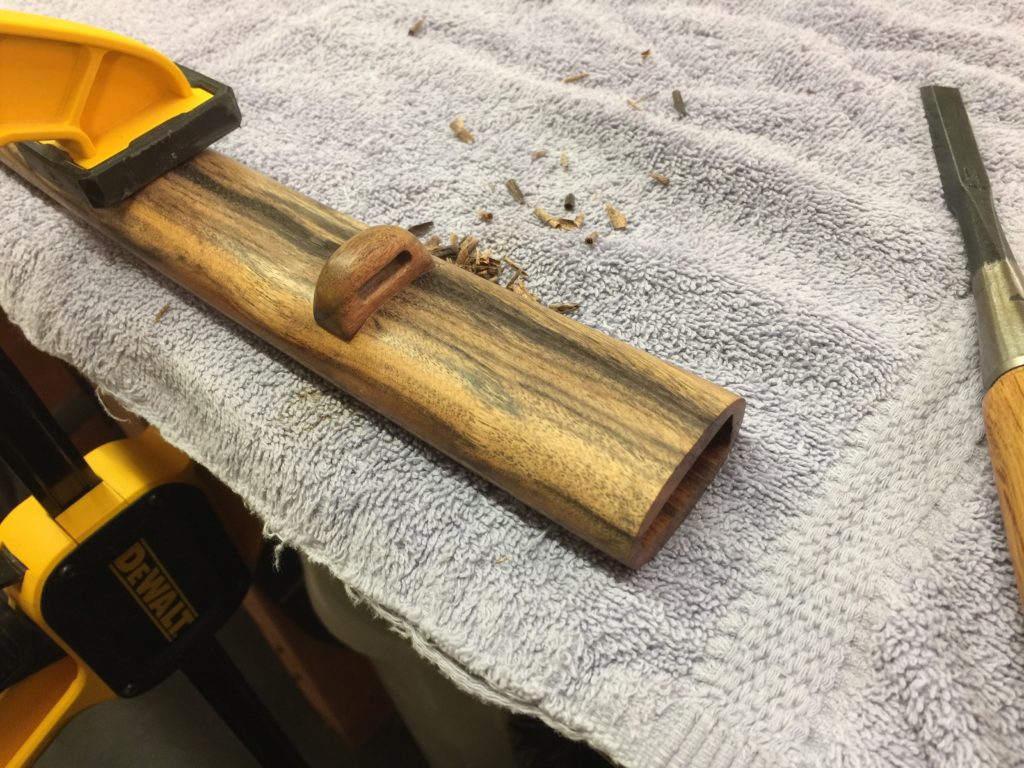
Attaching that kurikata is a delicate task. I needed to cut a nice flat groove in the saya, not too deep, and the exact thickness as the little knob I made. Sometimes these knobs are also made from buffalo horn; again, soft wood might split along the grain there as the knob will have a cord wrapped through it. But when you use hardwood like this, there’s little risk of it splitting.
The saya needs a couple coats of tung oil, my personal choice for any martial arts weapon made from wood, and it’ll be ready to go! Up next will be the finished sword.