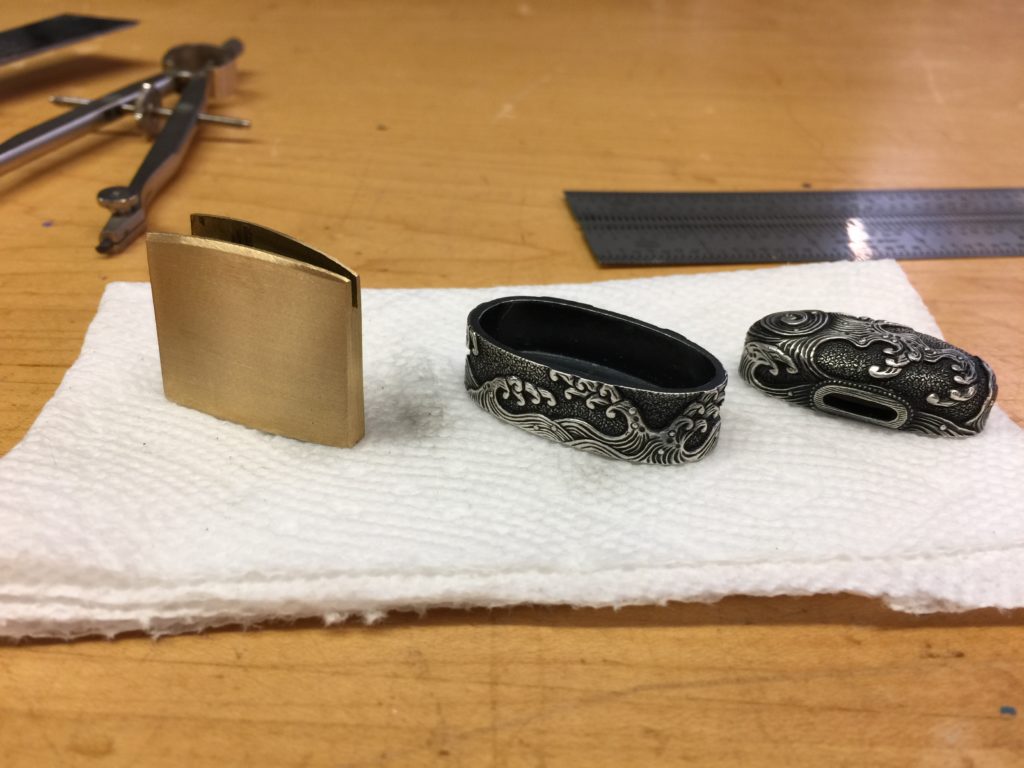
On the left is the brass habaki, the collar that holds the tsuba in place on the blade. To its right are the fuchi and koshirae, which cap the top and bottom of the handle. The habaki came with the blade and is fitted. The fuchi and koshirae are from Japan and I even had to pay for them in yen. You can find cheap ones on the internet and they are almost always of low quality, gaudy, made of crappy metals and full of flaws. These were not cheap but they are perfect. I like the black and silver color scheme and I love the waves. They will help give the sword its spirit.
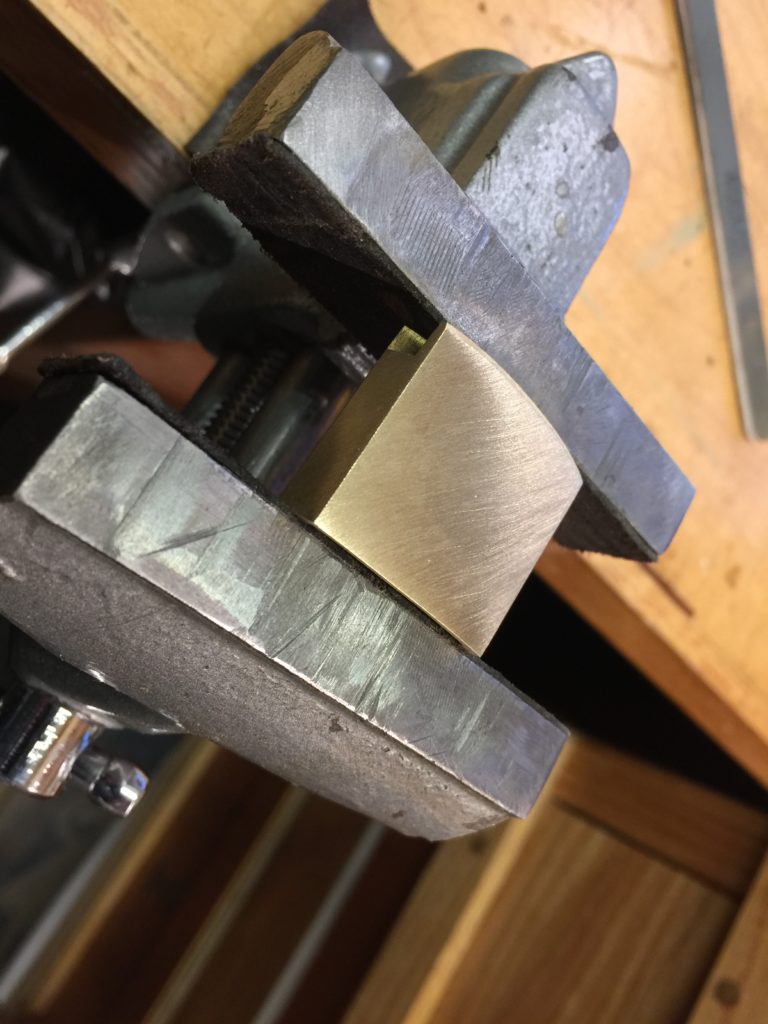
The brass habaki tends to rub on the saya (the wooden sheath) a bit when the sword is drawn, so it will take some wear and if you use your sword this is normal. So I don’t put a lot of polish on these, but I do some. Here I sand it with some coarse sandpaper in a diagonal grain.

I polish off the diagonal scratches on the top only, leaving them on the bottom to give it some interest.

Brass is a nice soft metal and is fairly easy to tool and polish, but it does burn through a lot of sandpaper!
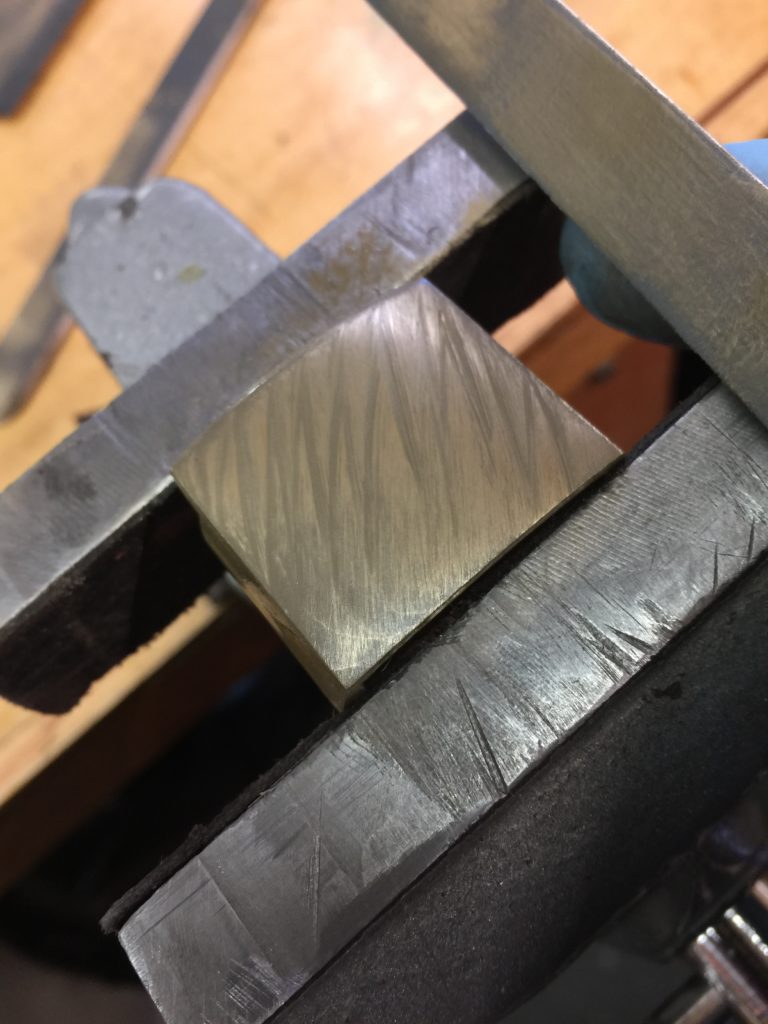
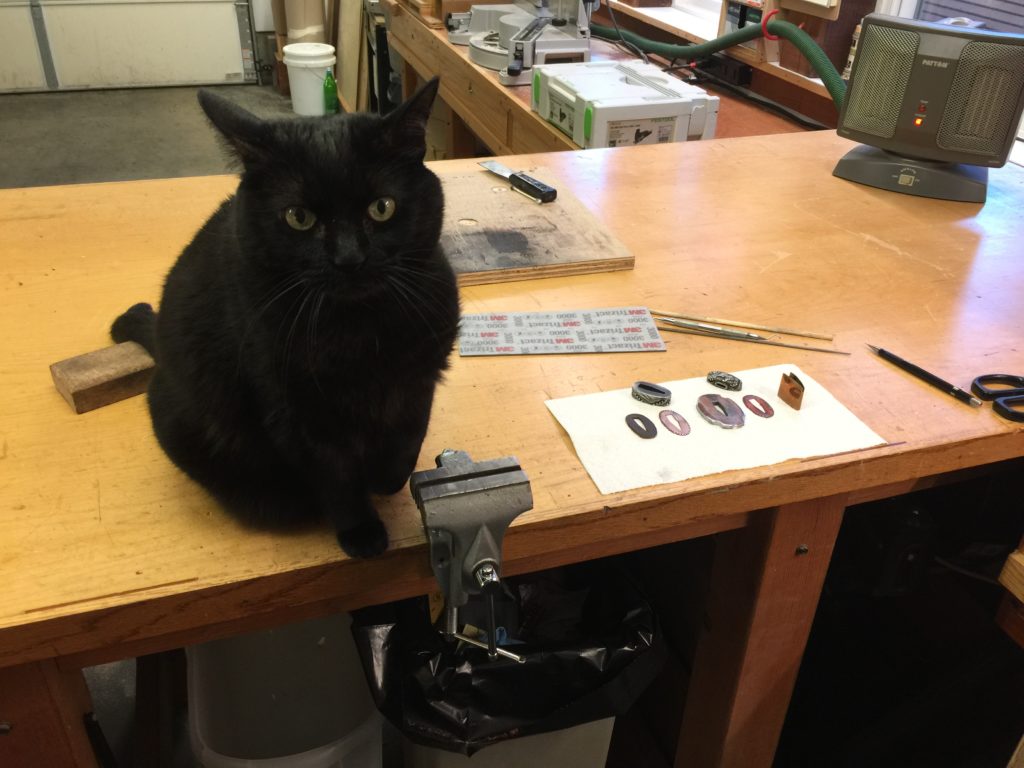
My assistant thinks they need a little more work, but I think they’re ready.

After polishing, I gave the habaki and the two copper seppa a little patina using sulfur and boiling water. The copper was absolutely blackened, which I had to polish off a little, but the brass habaki took on a complex reddish hue, which I thought looked nice. I also make a leather seppa, which is non-traditional, but it’s kind of nice to have between the handle and the tsuba, seems to absorb some shock and helps make a tighter fit.
Now I’m ready to make the handle.